Recent innovations are changing how drivers, technicians, and fleet managers approach repairs and maintenance for trucks. As trucks become more high-tech, the need for understanding and adapting to these new systems has never been more important.
In this article, we will explore:
- Telematics Systems
- Over-the-Air Updates
- Electric Truck Maintenance
- Driver Alerts and Fault Codes
- Cloud-Based Fleet Management
- Digital Maintenance Schedules
Telematics Systems for Predictive Maintenance
Telematics allows real-time monitoring of a truck's components, helping to predict issues before they escalate. With the rapid advancement of high-tech trucks, using telematics systems is no longer optional — it’s a necessity.
The Power of Telematics
Telematics systems provide fleet managers and drivers with crucial insights into vehicle performance. These systems monitor and analyze metrics such as:
- Engine Health – Track issues like misfires, overheating, or declining power.
- Fuel Efficiency – Monitor fuel consumption patterns and identify areas for optimization.
- Tire Pressure – Get alerts for low or high tire pressure to prevent blowouts.
- Battery Health – Prevent dead batteries and power failures.
- Brakes and Suspension – Detect wear and tear in critical components before they fail.
How Telematics Systems Work
A telematics system is a network of onboard sensors, GPS technology, and communication modules. These components work together to transmit real-time data from the truck to fleet management software, where it is analyzed for patterns and anomalies.
Here’s a breakdown of the process:
- Data Collection: Sensors monitor various systems (engine, tires, fuel, etc.) in real time.
- Transmission: Data is sent via cellular networks or satellite to a cloud-based platform.
- Analysis: The system uses algorithms to detect performance trends or errors.
- Alerts: If the system identifies a potential issue, such as a drop in fuel efficiency or overheating, it sends an alert to the driver and/or truck owner.
- Action: Maintenance is scheduled before the issue leads to breakdown or major damage.
Benefits of Predictive Maintenance
Using telematics for predictive maintenance offers advantages over traditional reactive approaches. These benefits extend beyond individual vehicles and can transform how fleets are managed:
- Cost Savings: Predictive maintenance helps avoid repairs and part replacements. Instead of changing components on a set schedule, you can wait until the data shows wear or performance decline. Fleets using predictive maintenance have reported an 8% reduction in overall maintenance costs.
- Longer Vehicle Lifespan: Regularly servicing your truck based on its actual condition, rather than intervals, helps keep it working longer. This can extend the lifespan of your vehicle by 20-30%.
- Safety: Catching potential issues before they become serious helps maintain safety standards. For example, if tire pressure dips below a safe level, telematics can notify drivers before it becomes a safety hazard on the highway.
Over-the-Air (OTA) Updates
In the past, software updates for trucks required a visit to a service center, where technicians would manually upload new software to the vehicle’s control systems. With over-the-air (OTA) updates, this process has become far simpler.
How OTA Updates Work
Over-the-air updates enable software changes to be delivered directly to the truck without it needing to leave the road. These updates can be sent via wireless connections, allowing trucks to receive necessary fixes or upgrades to their electronic systems while they’re in the field. This includes updates to engine control units (ECUs), safety systems, and telematics software.
OTA updates allow fleet managers to deliver software changes directly to trucks without needing to take them off the road. These updates are transmitted wirelessly, enabling trucks to receive:
- Engine Control Unit (ECU) upgrades – Boosting engine performance, fuel efficiency, and emissions controls.
- Safety System Improvements – Updating critical safety features like brakes, airbags, and Advanced Driver Assistance Systems (ADAS).
- Telematics Software Fixes – Ensuring smooth data transmission and performance tracking.
Impact on Repairs and Maintenance
OTA updates allow vehicles to stay on the road while receiving software improvements or bug fixes. These updates can also address known software issues that could affect vehicle performance or safety features. For instance, if a manufacturer discovers a glitch in the truck’s ADAS, they can push a fix remotely, ensuring that drivers are operating the safest and most up-to-date version of the system.
With wireless connections, trucks can receive these updates in the field, eliminating the need for time-consuming service appointments. In fact, fleets utilizing OTA updates have been shown to reduce service-related downtime by up to 80%.
From a maintenance perspective, OTA updates make it easier for fleet managers to ensure their trucks are running the latest software versions, preventing compatibility issues and improving overall vehicle performance.
Electric Truck Maintenance
Electric truck maintenance is becoming a big part of modern fleet management as more companies adopt eco-friendly transportation options. The importance of understanding the differences between electric and diesel truck maintenance is constantly increasing, as this knowledge ensures that fleets operate cost-effectively while meeting sustainability goals.
Here are the maintenance differences in powertrain and engines, batteries, braking systems, and exhaust systems:
Powertrain and Engine Maintenance
With no internal combustion engine, electric trucks eliminate the need for many traditional maintenance tasks. Say goodbye to oil changes, glow plugs, and timing belts. Instead, electric trucks rely on an electric motor, which has far fewer moving parts. Fewer moving parts mean fewer breakdowns and lower maintenance costs. A study by the North American Council for Freight Efficiency (NACFE) suggests that electric trucks can reduce maintenance costs by up to 50% compared to diesel trucks.
Battery Maintenance
Most electric trucks use lithium-ion batteries, which have an average lifespan of 8 to 10 years. Monitoring battery health, charge cycles, and ensuring proper cooling are key to maximizing this lifespan.
Fun fact: Tesla reports that its electric truck batteries degrade by just 10% after 200,000 miles. Regular battery checks, including inspections of the charging system and monitoring for any performance dips, help prevent expensive battery replacements down the line.
Braking System
Electric trucks come with a cool feature: regenerative braking. Instead of relying on friction to stop the vehicle, regenerative braking captures energy and uses it to recharge the battery. This means brake pads in electric trucks last much longer than diesel ones. Studies have shown that regenerative braking can extend brake life by up to 50%.
Exhaust System
Here’s one area where electric trucks shine: no exhaust system, no problem! Electric trucks produce zero emissions, which means no exhaust pipes or diesel particulate filters (DPF). This simplifies maintenance and helps you avoid the constant upkeep and cleaning associated with emissions systems in diesel trucks. It’s a win for your wallet and the environment.
Driver Alerts and Fault Codes
Modern trucks are equipped with advanced sensors and monitoring systems that constantly track the vehicle’s health. One of the most valuable tools is the ability to receive alerts when something goes wrong.
Key Benefits of Driver Alerts and Fault Code Notifications
- Fault Detection: Sensors continuously monitor engine performance, oil levels, tire pressure, brake wear, and more.
- Early Warning System: Notifications are triggered when a fault is detected for timely intervention.
- Cost Savings: Addressing issues early can save up to 30% on repair costs, according to a study by Fleet Maintenance.
- Enhanced Safety: Early alerts can prevent dangerous on-road failures, promoting a safer driving environment.
Understanding Fault Code Notifications
Fault codes provide data on your truck's health. For example, a low oil pressure alert may indicate a leak, while a high engine temperature warning could signal coolant issues. These codes are displayed directly on the driver’s dashboard or transmitted to fleet management systems.
Here’s a quick breakdown of common fault codes and their implications:
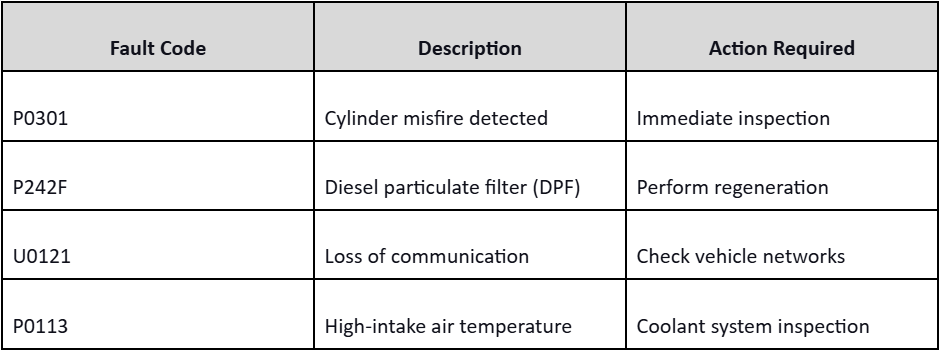
Reducing Downtime with Proactive Alerts
When a fault code alert is triggered, drivers can assess whether to continue driving or seek immediate assistance. According to data from the American Trucking Association, early fault detection can reduce maintenance costs by as much as 40%.
Pro Tips for Fleet Managers
- Analyze Trends: Use telematics to track recurring faults across the fleet.
- Schedule Maintenance Strategically: Plan repairs only when vehicles are off-duty.
- Stay Up to Date: With instant notifications, you can address issues quickly and lower disruptions.
Cloud-Based Fleet Management Systems
With advancements in cloud-based systems, fleet management has transformed into a streamlined, data-driven process that allows managers to monitor vehicles, manage maintenance schedules, and track overall fleet health from a centralized platform.
How Cloud-Based Fleet Management Works
Cloud-based systems collect and store data from each vehicle in the fleet, putting it into a digital dashboard accessible anytime, anywhere. Here’s how it benefits fleet managers:
- Accurate Monitoring: Instant access to vehicle health data, including fuel efficiency, engine performance, and fault codes.
- Maintenance Histories: Comprehensive repair records allow managers to review past repairs, identify patterns, and anticipate future maintenance needs.
- Predictive Analytics: Data insights help detect component wear trends.
Key Advantages of Cloud-Based Fleet Management
By consolidating data across the fleet, managers can take a more proactive stance on vehicle maintenance and make informed decisions.
- Cost Savings: Cloud-based systems can cut significant maintenance costs.
- Safety: Early detection and preventive maintenance reduce the risk of breakdowns, enhancing on-road safety.
- Productivity: Proactive maintenance scheduling minimizes unplanned downtime, improving fleet availability by up to 25%.
Proactive Maintenance Planning
Cloud-based fleet management platforms simplify proactive maintenance with intuitive data visualization tools, making it easy to track and schedule necessary servicing. By avoiding gaps in maintenance, you can enhance vehicle performance and ensure reliable, consistent operation across the fleet.
Key features include automated alerts for upcoming service needs, low tire pressure, and fluid levels, as well as reporting that offers insights into each vehicle’s health and maintenance expenses. These tools support data-driven budgeting and efficient resource allocation, allowing you to reduce costs and maintain a high-performing fleet with ease.
Digital Maintenance Schedules
Digital maintenance schedules are integrated with telematics systems or cloud-based fleet management software. They automatically track the mileage and usage of each truck, generating reminders when specific maintenance tasks — such as oil changes, brake inspections, or tire rotations — are due. You receive notifications via their dashboards or mobile apps, ensuring no service interval is overlooked.
The Benefits of Digital Maintenance
Staying on top of routine maintenance is critical for the longevity of a truck. Digital schedules reduce the risk of human error, such as forgetting a scheduled service, and ensure that each truck is maintained according to manufacturer guidelines. For fleet managers overseeing multiple vehicles, this technology provides peace of mind, knowing that all trucks in the fleet are in good operating condition.
Digital maintenance schedules help to standardize repairs across the fleet. If similar models or vehicles are used, fleet managers can apply consistent service intervals, making fleet-wide maintenance more predictable and cost-efficient.
Stay Ahead of the Curve
As technology continues to advance, the way heavy-duty trucks are repaired and maintained is evolving. These innovations are revolutionizing the industry, offering you tools to keep your trucks in top shape.
Adapting to these changes requires a proactive approach from everyone involved in the trucking industry. Technicians must stay current with evolving repair technologies, fleet managers need to embrace data-driven decision-making, and drivers must learn to rely on digital tools and alerts for vehicle maintenance.